Laboratory Support Development & Support
Our Services / HACCP / Laboratory Support
What is Laboratory Support?
A fully functional, accurately operated laboratory is essential for any food safety and quality assurance system. It provides critical data to verify that products meet safety standards, regulations, and industry best practices.
Laboratory support includes developing and validating testing methods, maintaining quality control programs, and troubleshooting analytical issues.
Effective lab management ensures that results are reliable, reproducible, and audit-ready.
Partnering with expert support helps streamline operations, enhances accuracy, and ensures compliance with USDA, FDA, and GFSI standards, thereby protecting product integrity and maintaining consumer trust.
Why Choose Our Laboratory Support Development?
Reach out to us today to elevate your laboratory capabilities and ensure your testing processes meet the highest standards. We provide comprehensive support services that align with USDA, FDA, and GFSI-recognized standards, including method validation, quality control procedures, and proficiency testing.
Our team of experts can help you design validation protocols, optimize testing workflows, calibrate equipment, and troubleshoot analytical issues. With our support, your laboratory will deliver consistent, accurate results, improve compliance, and be fully prepared for audits and inspections. Trust us to strengthen your testing program and protect your brand.
Validation & Testing Protocols
Developing, validating, and implementing reliable testing methods tailored to your specific products and matrices. This includes microbiological testing, chemical residue analysis, allergen detection, and sample preparation procedures aligned with regulatory standards. Validation ensures that testing methods produce accurate, consistent, and legally defensible results.
Supporting your laboratory with routine calibration, proficiency testing, oversight, and troubleshooting of analytical issues. Scheduled reviews and audits of testing processes help maintain high-quality, accurate results, strengthening your clinical compliance and facilitating quick responses to unexpected analytical challenges.
Quality Assurance & Troubleshooting
Laboratory Support offers technical services and expert guidance to ensure your testing processes are accurate, reliable, and compliant. This includes developing and validating customized analytical methods, routine equipment calibration, proficiency testing, troubleshooting, and ongoing process oversight. We also provide training and documentation to maintain accreditation, support audits, and promote continuous improvement, safeguarding product safety and enhancing your quality system.
Ready to Build a Stronger Food Safety Program?
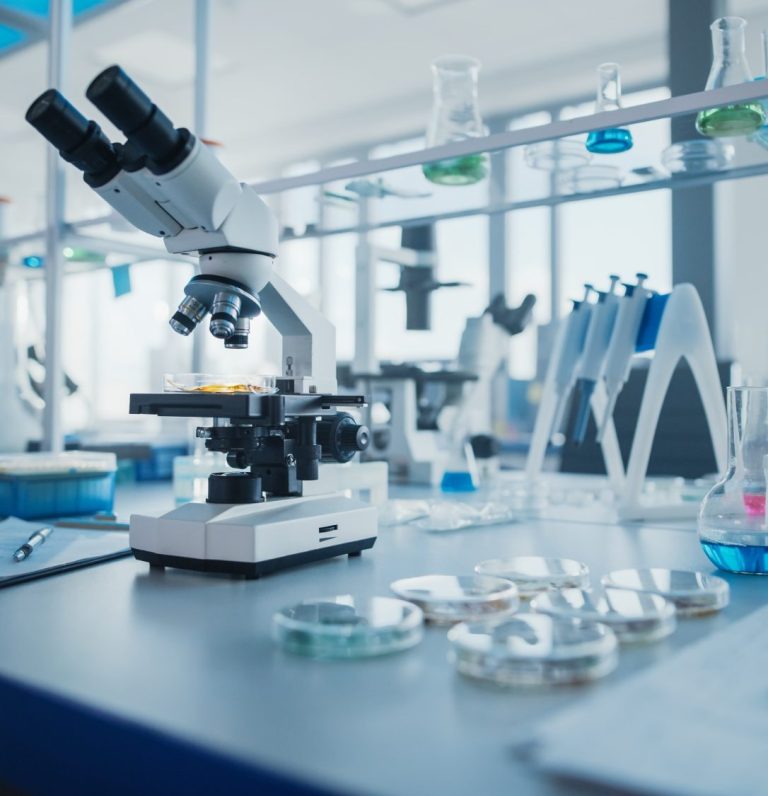
Creation
We can create your Laboratory Program aligned with industry standards, including GFSI-recognized schemes, USDA, and FDA regulatory requirements.
Our tailored solutions provide a strong foundation for compliance, operational efficiency, and industry performance, ensuring your programs are scalable and audit-ready.
Gap Analysis
Our thorough assessments identify weaknesses in your current processes and systems, whether related to GFSI standards, USDA, or FDA regulations.
By pinpointing vulnerabilities early, we enable you to proactively address gaps, strengthen your compliance posture, and prepare effectively for audits or certification processes.
Implementation
Our team supports seamless integration of new or existing programs, ensuring they meet industry standards such as GFSI, USDA, and FDA.
We assist in training staff, establishing procedures, and embedding controls into daily operations—helping you achieve system integrity and regulatory readiness.
Wherever You Are in the Process, We've Got You Covered
Training & Support
We empower your team with customized training programs focused on GFSI, USDA, or FDA compliance requirements.
Our ongoing support ensures your programs are maintained properly, fostering a strong culture of food safety, continuous improvement, and regulatory adherence.
Validation
We confirm that your controls, processes, and systems are effective through science-based validation tailored to GFSI schemes, USDA, or FDA standards.
Our validation services help reduce risks, demonstrate ongoing compliance, and support continuous improvement in your food safety and quality management systems.
Contact us for your free consultation today
Laboratory Support Documentation
Our HACCP Flow Chart Services
At Points North Certified, we provide a comprehensive suite of laboratory support documents designed to optimize your testing systems, ensure regulatory compliance, and bolster your product safety. These tools facilitate effective management of laboratory operations, validation of testing methods, and continuous improvement in analytical practices. Whether you're establishing new laboratory processes, closing gaps, or validating critical parameters, our tailored documentation supports accurate testing, reliable results, and seamless audit preparation.
Laboratory Program
A detailed framework outlining your laboratory’s objectives, scope, policies, and procedures for testing and analysis to ensure consistent, compliant operations.
Internal and External Laboratory Gap Analysis
A thorough assessment identifying strengths and weaknesses in your current testing practices, with recommendations for improvement and alignment with industry standards.
Lab CCP Testing
Protocols for testing at Critical Control Points, ensuring key parameters are monitored accurately to control hazards related to microbial, chemical, or physical contamination.
Custom Product Testing Plan/Schedule
A tailored plan outlining required tests, frequency, and key parameters for each product or process to support safety and quality verification.
Testing Methods and Protocols
Scientifically validated testing procedures and protocols that ensure accurate, reproducible results compliant with regulatory and industry standards.
Analysis of Critical Parameters
Identification and monitoring of critical parameters—such as pH, temperature, or microbial counts—that directly impact safety and quality, with documented analysis and review.
Corrective Actions
Step-by-step procedures to address testing deviations or failures, including root cause analysis and implementation of corrective measures.
Preventative Actions
Strategies to prevent testing failures or accuracy issues, supporting ongoing validation, and continuous quality improvement.
Training and Competency Policies
Programs and documentation to ensure staff are trained, competent, and up-to-date on testing methods, safety protocols, and standards.
Laboratory Sourcing (If applicable)
Guidance on selecting and managing external laboratories, including qualification criteria, service standards, and ongoing performance evaluation.
Internal Laboratory Build-Out Plan (If applicable)
A strategic plan outlining steps, resources, and timelines for developing or upgrading your internal laboratory facilities.
Internal Validation Checklists
Tools for verifying that laboratory testing methods, equipment, and procedures are validated according to accepted standards before routine use.
Helpful Links
Experienced Industry Experts
Our team brings decades of hands-on validation experience across multiple food sectors, including meat & poultry, baked goods, snack foods, beverages, and more.
Support & Continual Improvement
We provide guidance for ongoing validation activities, re-validation schedules, and performance monitoring to sustain food safety over time.
Detailed and Clear Documentation
Our validation reports and protocols are comprehensive, transparent, and designed to support your internal records, external audits, and regulatory inspections.
Regulatory & Certification-Ready
We tailor validation procedures to meet FDA, USDA, GFSI, and other relevant standards, ensuring your processes are audit-ready and certification compliant.
Our relationship doesn’t end once your programs are created. We offer ongoing support, help monitor performance, and review your systems periodically to identify areas for improvement, ensuring your food safety practices stay current and effective.